Would you like to explore our corporate site or visit your local website?
Stay on Corporate siteAbout three years ago, KONE service technicians in the Netherlands started making noise about the amount of waste materials they had to deal with as part of their daily routines. Their concerns resonated with KONE’s Global Spares Supply (GSS) unit, which acts as a centralized internal supply unit for spares, providing parts for KONE’s Service Business around the world.
They set out to work with the Dutch team to study various solutions. One of them was to replace the single-use cardboard boxes conventionally used in spares deliveries to the service technicians with lightweight, stackable, reusable plastic boxes that allow for reductions in or even the complete elimination of packaging materials. What’s more, the recyclable crates enabled the adoption of a new, centralized waste disposal process that eliminates emissions further.
Magic boxes
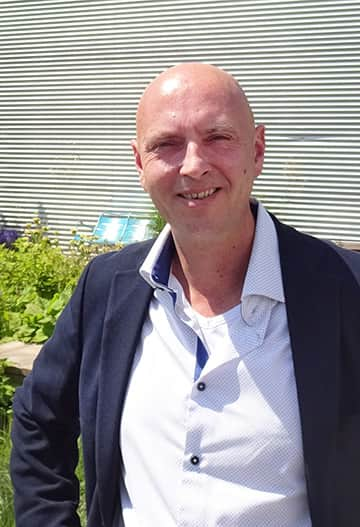
Jacques van Hettema, unit sourcing manager at KONE Netherlands, is eager to sum up the advantages of the pilot that was set up to test the plastic crates and the new operating model.
“We looked at several logistical processes. We found that we are able to consolidate the weekly, overnight deliveries by a third-party carrier in the Netherlands to the technicians. In addition, the boxes don’t require the use of carton or foam filling materials. Plus, we implemented a waste return system using the same boxes.”
Van Hettema notes that the circular process is straightforward, not to mention efficient. Here’s how it works: The service technician fills the box with any remaining packaging materials and damaged parts after a job. The crates are collected from the service technician’s car and returned to the central distribution center in Voorschoten in western Netherlands. Here, there are several containers on site for the different kinds of waste and parts that are returned for disposal or recycling. Every box has a unique code, which is scanned and linked back to the service technician, making it easy to track the boxes and keep them in circulation.
“The service technician will never be without the box and the materials required for a service call,” says van Hettema. “Since KONE’s central European warehouse is based in Germany, our weekly, overnight shipments take max seven hours by car. The service technician no longer has to drive to several locations to dispose of packaging materials or damaged parts, so this reduces our greenhouse gas emissions tremendously.”
Next steps
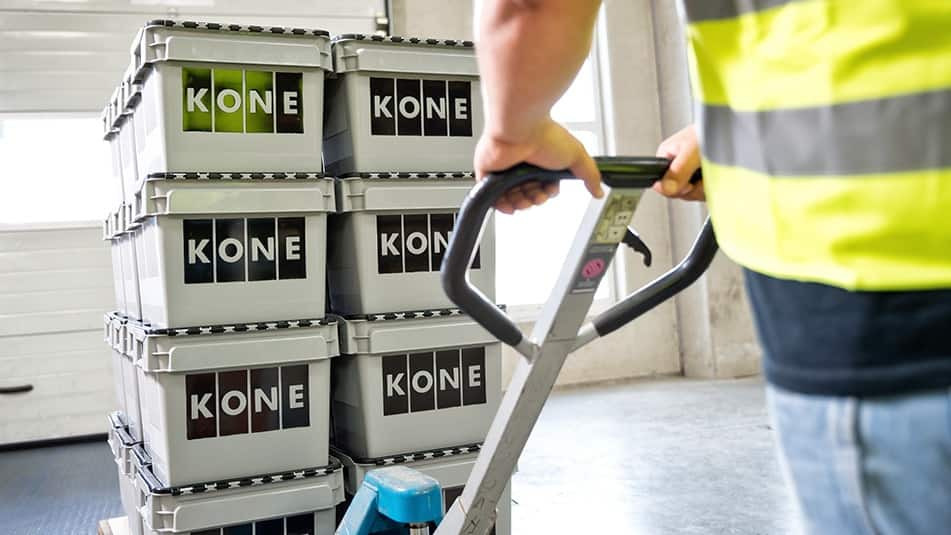
The Dutch pilot project went live in early June 2019, about the same time a huge storm hit the Netherlands. “No worries, our boxes are waterproof and can be tightly secured to the backseat of the car with a seat belt,” van Hettema laughs. The pilot’s success has led to all 250 KONE Netherlands elevator service technicians now using the boxes.
“We will closely monitor their findings, and if everything works according to plan, we can also apply this process to our escalator and automatic door service technicians,” says van Hettema.
Globally, KONE is planning to take this circular business model to the next level by bringing it to other countries and also expanding it to other modes of transport.
“This delivery process, combined with returns through the same flow and the centralized disposal of waste, allows us to significantly reduce packing waste, the time our technicians spend driving around in their cars, and thus also our greenhouse gas emissions,” says Anselmi Tuominen.
In his role as KONE’s materials management process owner for the Maintenance Business and GSS Global Operations, Anselmi has worked closely with the Dutch team on this pilot and is excited by the prospect of further reducing KONE’s environmental impact by expanding the model in the first phases to other central European countries.