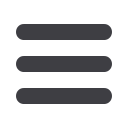
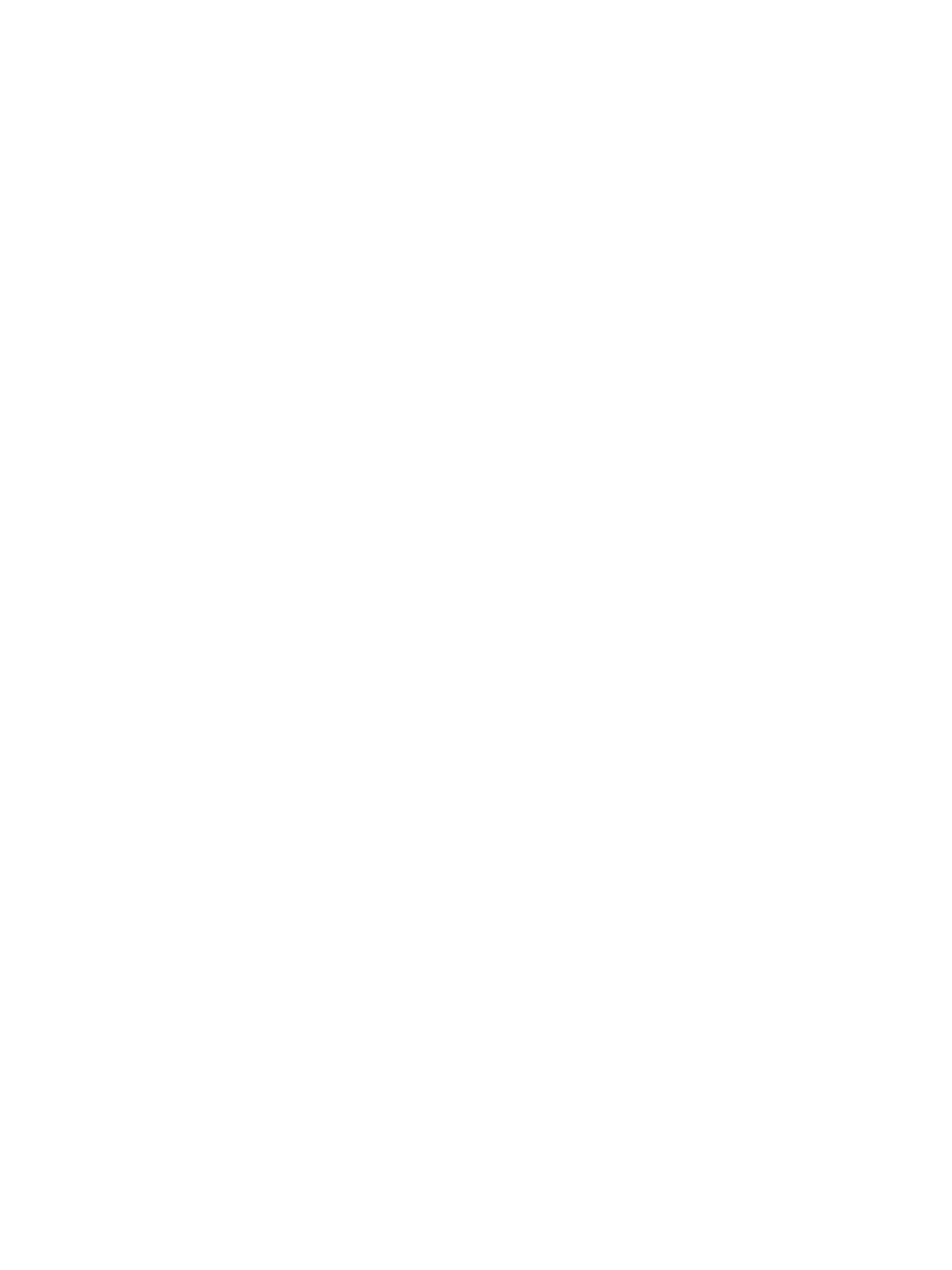
16
| PEOPLE FLOW
A
s the mechanical driving
force behind the KONE
MonoSpace
®
elevator,
KONE EcoDisc was the
first design of its kind to
allow an entire hoisting system to be
housed within the elevator shaft itself.
Remarkably, explains
Eero Keskinen
,
Director of Hoisting Machines, KONE
EcoDisc was the most eco-efficient
hoisting motor to exist in any industry
at that time.
“We were the very first to patent the
machine room-less hoisting system,”
Keskinen states. “It was a real break-
through in this field of engineering.
There were no intellectual property
limitations. Our engineers were free to
design the optimal system.”
The obsolescence of the separate
machine room opened up a new realm
for architects and designers, and the
entire industry has since followed suit.
Other companies have attempted to
mirror KONE EcoDisc’s success, but
the disc-shaped creation remains hard
to beat in terms of its efficiency and
adaptability.
“The motor is so thin that engineers
have nicknamed it pancake motor,”
Keskinen quips. “It reduces demands
on building space and load, allowing
text
Sarah Hudson
Illustration
KONE
A new age in
elevator engineering
designers more room to create elevator
designs that enhance the ride quality for
passengers.”
New technology drives
development
Sixteen years down the line, the
company launches its second
generation KONE EcoDisc, adding
numerous technological advancements
to a system that remains a benchmark
in the industry. The completely renewed
hoisting motor and drive system deliv-
ers greater energy efficiency, helping to
reduce both operational costs and
a building’s carbon footprint.
“The energy loss from energy that
is not transformed into useful work has
been reduced by one-third relative to
the 2010 design,” explains Keskinen.
What this means for building owners is
substantial monetary savings over the
lifespan of the elevator, he points out.
Improved maintenance efficiency is
also significant to the updated design,
especially in terms of the braking sys-
tems and the motor control equipment.
“The essential parts of the motor
are, in fact, very low-maintenance for
all standard elevator applications.”
Keskinen adds, “The motion control
design does not have bearings or other
wearing components, resulting in a
practically unlimited lifetime for the
system. Additionally, the stopping accu-
racy remains exceptional over time and
use, due to the firmly mounted sensor.”
No middle ground
The low-maintenance design makes a
notable difference to the optimization
and positioning of components, as tech-
nicians no longer require access to parts
of the motor they once would have.
Furthermore, it allows for ample safety
margins, with far greater ability to deal
with all the forces and stresses imposed
on the system.
“The compact nature of the motor
allows for a rigid design structure – a
factor in terms of safety. Safety is the
starting point for every piece of KONE
equipment, and we’ve built on our
knowledge and understanding of these
priorities in the new generation of the
KONE EcoDisc product,” says Keskinen.
As the technical limitations of hoist-
ing systems become less of an issue, the
comfort of the user has gained greater
attention, becoming a key driver for
design. Innovation is increasingly focus-
ing on minimization of sound and vibra-
tion, and any audible or tactile sense of
movement or impact. Compared to its
The KONE EcoDisc
®
hoisting motor set new standards in 1996 for
elevator hoisting in terms of performance, space savings and accuracy.
Over a decade and a half later, KONE redesigns its hoisting motor to
deliver best-in-class energy efficient performance.