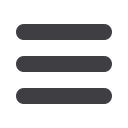
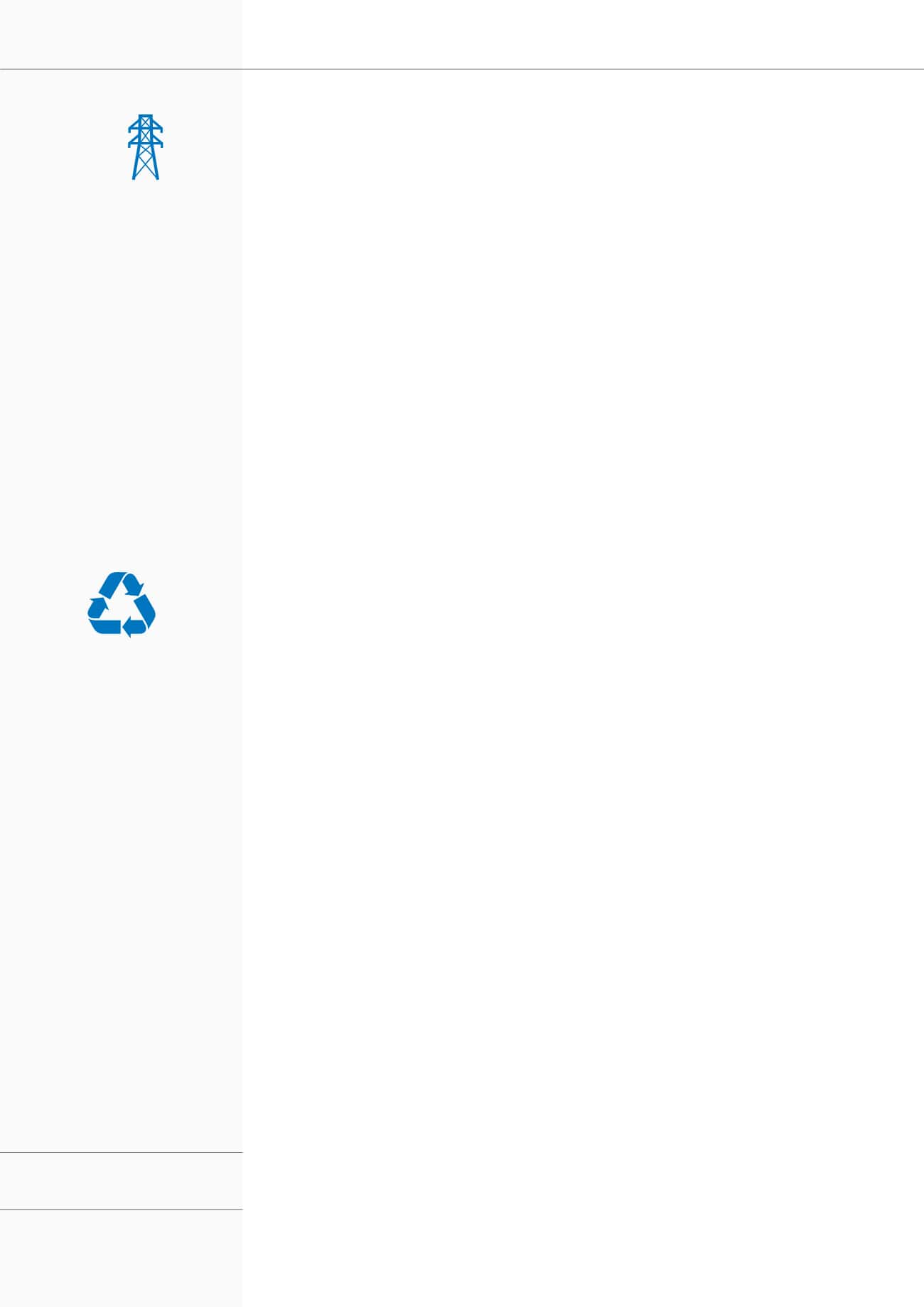
KONE 2015 | SUSTAINABILITY REPORT
ENVIRONMENT - OPERATIONS
28
Read more
about KONE’s product carbon
footprint on p. 24.
100%
of the electricity consumed at KONE’s
corporate head offices and the whole
manufacturing and R&D site in
Finland is produced by wind power.
Other KONE units that purchase
green electricity are our Belgian,
German, Swedish, and Danish country
organizations. KONE’s manufacturing
unit in Slimpa, Italy, has a solar energy
system that produces around 5% of
the electricity the unit consumes. The
LEED Platinum certified KONE US
Operations Center in Moline, Illinois,
has over 1,300 solar panels that
produce around 30% of the electricity
consumed by the facility.
0%
landfill waste at escalator
manufacturing unit and GiantKONE
in China, manufacturing units in
Chennai, India, Hyvinkää, Finland,
and Pero, Italy.
Electricity
Electricity and district heat consumption
accounted for 40 ktCO
2
e (2014: 41) or 13% of
KONE’s operational carbon footprint in 2015.
The electricity was used in KONE’s offices,
warehouses, and manufacturing facilities. The
figures take into account our usage of green
electricity produced using renewable sources
(market-based calculation method). Without the
use of green electricity (location-based method),
the electricity carbon footprint would have
amounted to 43 ktCO
2
e (2014: 44). The share
of green electricity increased to 22% in 2015
(2014: 20%). In 2015, electricity consumption
was 79,800 MWh (2014: 79,900) and the
consumption of district heat 15,100 MWh
(2014: 15,900). The absolute electricity carbon
footprint decreased by 2.9% and the relative
footprint by 8.2%.
KONE’s Global Facility Policy includes
energy saving targets. During 2015, KONE’s
manufacturing unit in Italy achieved the ISO
50001 Energy Management System certification
as the second KONE unit. Our manufacturing
unit in the Czech Republic was the first KONE
unit to be certified in 2013. During the year,
KONE units falling into the scope of the new
Energy Efficiency Directive completed energy
audit reports or other related requirements
in eight European KONE countries. In two
additional countries where the local KONE
company would fall into the scope of the
directive (Spain and Poland), the directive was
not yet implemented locally.
Heating fuels and cooling gases
Heating fuels and cooling gases account for
4% of our operational carbon footprint. In
2015, fuels for heating and cooling generated
11 ktCO
2
e (2014: 11) of greenhouse gas
emissions.
Material management
In 2015, KONE used 722 k tonnes (2014: 682)
of materials for producing and packaging its
elevators and escalators. The figures have been
calculated based on life-cycle impact assessment
data. Higher material consumption figures
reflect an increase in production volumes. At
KONE, we focus on material management and
the optimization of our own operations. Our
primary goal is to achieve material efficiency
throughout our manufacturing chain, beginning
with the product development stage.
Waste optimization in
the manufacturing chain
In 2015, waste accounted for 2.5 ktCO
2
e
(2014: 2.3) or 0.8% of KONE’s operational
carbon footprint. We aim to reduce the waste
generated by our manufacturing processes
and offices through reduction at the source,
reuse and recycling, and by sending waste
to incineration. Landfill waste is kept to a
minimum. Waste is always handled according
to applicable laws and regulations in local
KONE organizations, and we aim to exceed
legal requirements.
Based on environmental data collected from
12 KONE engineering and manufacturing sites,
91% of the waste generated by KONE’s global
delivery chain was recycled or incinerated. Only
9% (2014: 8%) was landfilled. All of the waste
generated by our escalator manufacturing
unit and the GiantKONE manufacturing unit
in China and by our manufacturing units in
Chennai, India, Hyvinkää, Finland, and Pero,
Italy, is either recycled or incinerated – none is
landfilled. Only 0.3% of the waste generated
by our elevator manufacturing unit in China is
landfilled.
Water consumption
Water consumption in KONE’s production and
maintenance processes is minimal, and we
continue to optimize and further minimize our
usage of water. KONE uses municipal water,
and waste water is released into municipal
treatment systems that abide by local
regulations. The total amount of water used
in our manufacturing and office facilities was
390,000 m³ (2014: 390,000). In 2015, KONE’s
manufacturing units, excluding GiantKONE,
released 17 tonnes (2014: 20) of waste water
effluents into the municipal waste water
systems.