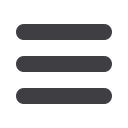
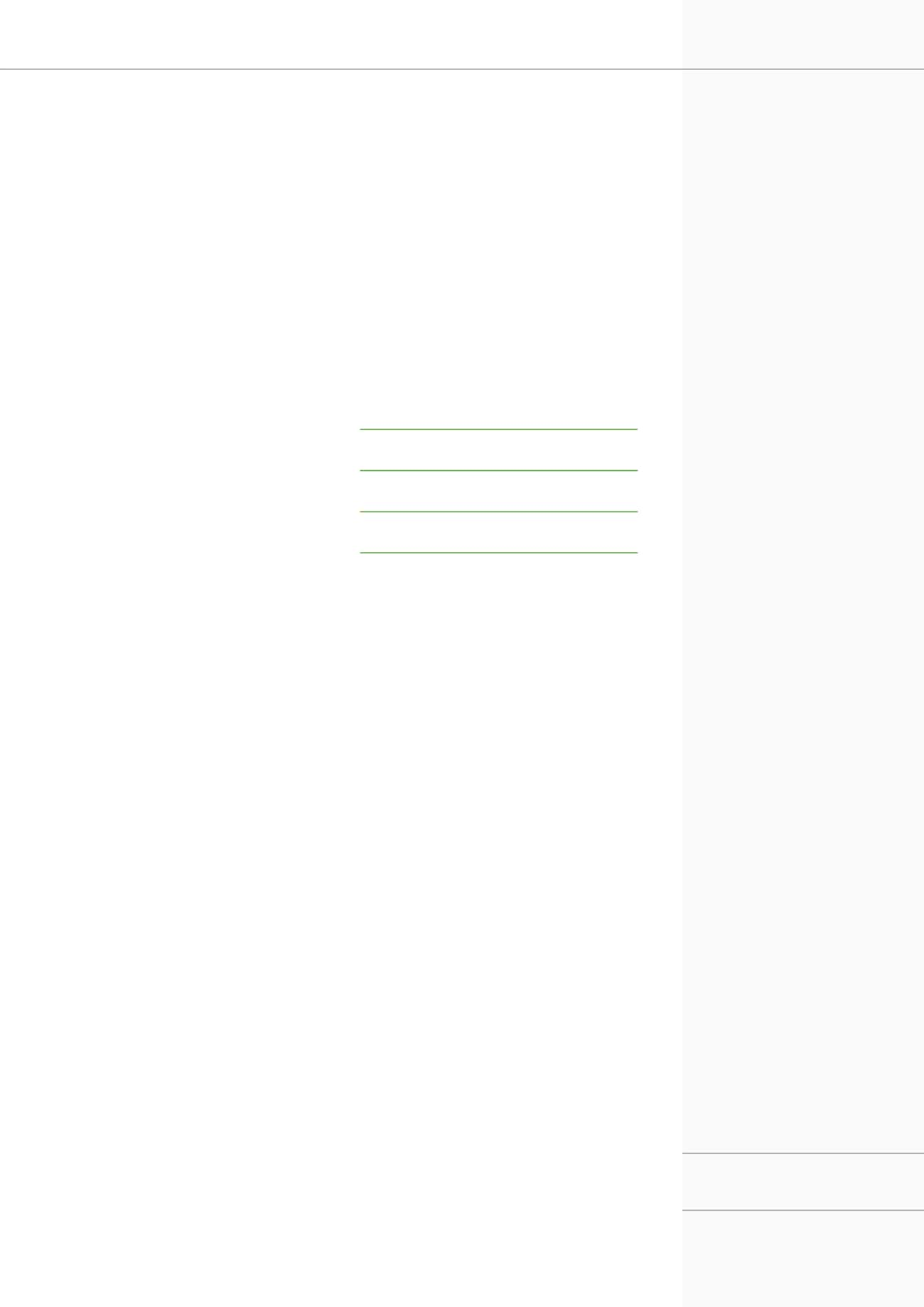
KONE 2015 | SUSTAINABILITY REPORT
31
QUALITY
Solution creation quality
KONE’s new solutions are screened during
the early stages for quality, using quality
management tools and thorough verification
processes. In the design stage we define critical
quality parameters that all solutions must fulfill
in order to proceed to production.
Delivery and manufacturing quality
KONE is working to continuously improve
its delivery chain in terms of quality,
responsiveness, and efficiency. We make sure
that we deliver to the highest quality standards.
In 2015 KONE started a project aimed at
improving in-house production quality. The
10x Better Factory project will harmonize
process control activities in our own production
lines further. As part of the project, solid and
up-to-date process control plans will be created
for each workstation, and critical standard
processes will be governed through real-time
statistical process control. The project enables
production unit employees to improve their
quality-related competences.
During the review year we carried out thorough
analyses of all of our production lines and
established global, in-depth production quality
guidelines to direct our production units on
their quality improvement journey.
In 2016 we will build production quality
competencies through eLearning materials
and local classroom trainings at all of our
production sites.
We have high standards for supplier quality. We
focus on ensuring our suppliers have excellent
manufacturing processes and process controls in
place.
KONE’s installation process quality enables us
to monitor the installation quality at different
stages of the process. We take corrective
KONE’s processes fulfill ISO 9001 quality
management system requirements.
All KONE’s corporate units, manufacturing units and R&D units are
ISO 9001 certified
28 of KONE’s major country organizations are ISO 9001 certified
97% of KONE’s strategic suppliers are ISO 9001 certified
action if needed during installation, and
conduct thorough quality tests to monitor the
outcome.
Maintenance quality
At KONE we are constantly working to maintain
the highest quality of service, and to keep
equipment in top condition for the best possible
user experience. KONE maintenance delivers
industry-leading customer value and quality.
We service close to 1.1 million elevators and
escalators. We offer our expertise throughout
the entire lifecycle of a building as maintenance
and modernization are tailored to maximize
equipment performance.
KONE develops a unique maintenance plan
for each piece of equipment. Each technical
module is maintained at appropriate intervals.
This enhances quality and end-user safety, and
minimizes equipment downtime.
Clear procedures for call handling, strong,
real-time support from the KONE Customer
Care Center, and detailed reporting and quality
control on every site visit guarantee quality in
everything we do. About 50 training hours per
person per year give KONE service technicians
the latest technical knowhow of the equipment
they maintain.
Read more about KONE’s
- supply chain on p. 42
- suppliers on p. 44
COMPREHENSIVE RIDE
COMFORT TEST
KONE elevators are tested for ride
quality, a service that is unique to
KONE. The test measures noise as well
as lateral quaking and vertical vibration
levels inside the car, and ensures
that our elevators provide a smooth
ride with minimum disturbance to
building occupants. After test results are
analyzed, improvements are made if
needed. This thorough testing reduces
the need for unplanned maintenance
callouts.
QUALITY ACHIEVEMENTS
• In our annual employee survey,
Pulse, the questions about quality
received high scores and improved
from the previous years.
• We audit all of the main suppliers
that deliver direct materials to KONE
distribution centers or factories on a
regular basis.